PCBA板加工是現代電子制造中的核心環節。它將元器件安裝到印刷電路板(PCB)上,通過焊接和測試,形成具有特定功能的電子模塊。由于PCBA板加工涉及多個步驟和工藝,因此需要遵循嚴格的規則以確保產品質量和生產效率。
以下是PCBA板加工過程中需遵循的一些關鍵規則:
一、設計規則
1. 設計優化:在開始PCBA加工之前,必須進行詳細的電路設計和布局優化。設計者應考慮到元器件的布局、布線密度、焊盤大小、過孔設計等因素,以確保信號完整性和電磁兼容性。
2. 可制造性設計(DFM):設計必須符合可制造性原則,以簡化生產流程,降低制造成本。應避免復雜的走線和狹小的焊盤,同時考慮元器件的可訪問性和可維護性。
二、材料選擇規則
1. PCB板材選擇:根據產品的應用領域和工作環境,選擇合適的PCB基材(如FR4、陶瓷、金屬基材等)。同時考慮板材的厚度、層數和表面處理方式(如HASL、ENIG等),以滿足電氣性能和耐環境性的要求。
2. 元器件選擇:元器件的選擇應符合設計規格和可靠性要求,并確保其尺寸、引腳形狀與PCB板上的焊盤匹配。此外,應選擇具有良好可追溯性和穩定供貨的供應商。
三、生產工藝規則
1. 焊膏印刷:焊膏印刷是SMT工藝的關鍵步驟。必須嚴格控制焊膏的厚度和分布,確保焊膏均勻覆蓋焊盤。使用專業的網板和印刷機,定期檢查和清潔網板,避免焊膏污染。
2. 元器件貼裝:元器件貼裝應采用高精度的貼片機,確保元器件準確放置在指定位置。對于不同類型的元器件,應調整貼裝機的壓力、速度和吸嘴,以避免元器件損壞或偏移。
3. 回流焊接:回流焊接是SMT加工的核心步驟。焊接溫度曲線必須精確控制,確保所有焊點充分熔化并形成可靠的焊接連接。焊接后應檢查焊點的質量,確保無虛焊、連焊、冷焊等缺陷。
4. 波峰焊接:對于DIP元器件,波峰焊接是常用工藝。必須確保焊接溫度和速度的穩定,避免焊錫不足或過多。對于焊接后的板件,應進行目視檢查或自動光學檢測,確保焊點質量。
四、檢測與質控規則
1. 光學檢測(AOI):在貼裝和焊接完成后,應通過AOI設備進行全面的光學檢測,識別元器件的缺失、錯貼、偏移、焊點缺陷等問題。AOI檢測能夠有效提高檢測效率和精度,是確保產品質量的重要手段。
2. X射線檢測:對于高密度BGA、CSP等封裝元件,X射線檢測能夠檢查焊點內部的連接質量,發現潛在的開路、短路、空洞等缺陷。特別是在檢測雙面PCB時,X射線檢測能夠提供更直觀的內部結構分析。
3. 功能測試:在完成所有物理連接后,需進行功能測試,驗證PCBA板的各項功能是否按設計要求正常工作。這包括電源測試、信號測試、通信測試等。功能測試能夠及時發現并排除潛在的功能性問題。
五、環境控制與防護規則
1. 靜電防護(ESD):在PCBA加工過程中,靜電可能對敏感元器件造成不可逆的損壞。因此,必須在生產區域內嚴格執行靜電防護措施,如佩戴防靜電手環、使用防靜電工作臺和地墊,并控制空氣濕度。
2. 清潔與包裝:焊接和測試完成后,應對PCBA板進行清潔,去除助焊劑殘留物,避免對電氣性能的影響。包裝時,應使用防潮、防靜電包裝材料,并在包裝前檢查PCBA板的外觀和清潔度,確保產品在運輸和儲存過程中不受損壞。
六、質量管理規則
1. 全程質量監控:PCBA板加工的每個環節都需建立嚴格的質量監控流程,從原材料驗收到成品出廠,都需經過多道質檢工序,以確保產品的可靠性和一致性。
2. 持續改進:在PCBA板加工過程中,應定期評估和優化生產流程,采用新的工藝和技術,以提高生產效率、降低成本,同時提升產品的質量。
總結來說,PCBA板加工是一個高度復雜和精細的過程,涉及多個關鍵步驟和工藝。遵循上述加工規則,可以確保PCBA板的質量和可靠性,滿足設計要求和行業標準。
深圳宏力捷電子是有著20余年PCBA加工經驗的PCBA代工廠,工廠配備多條SMT生產線、DIP生產線,可提供從PCB設計、電路板制造、元件采購、組裝、焊接、測試和最終交付成品電子產品的一站式PCBA代工代料服務。
深圳宏力捷推薦服務:PCB設計打樣 | PCB抄板打樣 | PCB打樣&批量生產 | PCBA代工代料
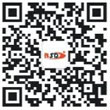