隨著電子產品向小型化、高集成度方向發展,SMT(表面貼裝技術)已成為現代電子制造的主流工藝。與此同時,電子元件作為成本較高且對工藝要求嚴格的關鍵材料,其損耗問題直接影響產品質量和生產成本。因此,如何在SMT加工生產中有效控制元件損耗,成為提升生產效率和經濟效益的關鍵所在。
一、電子元件損耗產生的主要原因
在SMT生產過程中,元件損耗主要源自以下幾個方面:
- 設備因素
設備精度不足、長期使用后老化、維護不當或參數設置不準確,均可能導致貼片機送料失誤、元件放置偏差,進而引發損耗。
- 人為操作失誤
生產操作過程中,因操作人員缺乏培訓或執行不規范(如料帶裝載不當、標識混淆、錯誤操作流程等)容易造成元件錯誤取放或損壞。
- 物料本身及包裝問題
部分元件因包裝不合理、存儲環境濕度過高或靜電防護不到位,易出現氧化、受潮或靜電損傷現象,影響后續貼裝質量。
- 工藝參數與流程缺陷
焊膏印刷不均、貼裝壓力與速度設置不當等工藝參數問題,均可能在貼片過程中造成元件定位不準確和損耗增加。
二、控制電子元件損耗的關鍵措施
為降低SMT生產中的元件損耗,企業可從以下幾個方面著手優化:
1. 嚴格的物料管理與倉儲控制
- 標準化物料驗收與入庫
對進廠物料進行嚴格的質量檢測與數量清點,確保包裝完整,杜絕不合格產品進入生產線。
- 科學的倉儲管理
按“先進先出”的原則管理庫存,并對倉庫溫濕度進行實時監控,確保元件存放在干燥、防靜電的環境中。同時,建立清晰的物料標識系統,避免因混料造成損耗。
2. 設備維護與工藝參數優化
- 定期維護與校準
保證SMT貼片機、送料器等關鍵設備定期保養和校準,保持設備處于最佳狀態,減少因設備故障引起的元件損耗。
- 工藝參數的精細化管理
根據不同元件特性,合理設置貼裝速度、壓力和角度,并定期檢查焊膏印刷模板,確保焊膏均勻、精確印刷,從源頭上降低損耗風險。
3. 提升操作人員技能與執行標準化作業流程
- 專業技能培訓
定期對操作人員進行系統培訓,使其熟悉設備操作規程、物料裝載與檢查標準,減少因人為操作不當導致的元件損耗。
- 嚴格執行標準作業流程
制定并落實詳細的作業指導書,明確各環節責任,實施首件檢驗、自檢、互檢及巡檢制度,確保每一道工序都能嚴格控制質量。
4. 引入先進檢測系統與數據反饋機制
- 自動化檢測設備應用
在生產線上引入AOI(自動光學檢測)、SPI(錫膏檢測)等自動化檢測設備,對貼裝質量實時監控,及時發現并糾正問題。
- 數據化管理與持續改進
利用MES等系統收集生產數據,對關鍵工藝參數和損耗數據進行分析反饋,及時調整優化工藝,形成持續改進的良性循環。
三、總結
通過完善物料管理、加強設備維護、優化工藝參數、提高操作人員技能以及引入自動化檢測系統,可以有效降低SMT生產中電子元件的損耗。這不僅有助于提高產品質量和生產效率,還能在激烈的市場競爭中為企業節約成本,增強核心競爭力。
四、關于我們的SMT貼片加工服務
深圳宏力捷電子擁有20余年的PCBA加工經驗,配備多條先進的SMT貼片及DIP生產線,具備從PCB設計、電路板制造、元件采購、組裝、焊接到最終成品交付的一站式代工代料服務。我們在控制元件損耗、優化生產工藝和提升產品質量方面擁有成熟的技術和嚴格的管理體系,期待與您攜手打造高效穩定的電子制造解決方案。如您有相關需求,歡迎隨時聯系我們,了解更多關于SMT貼片加工的專業服務信息!
深圳宏力捷推薦服務:PCB設計打樣 | PCB抄板打樣 | PCB打樣&批量生產 | PCBA代工代料
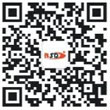