PCB板面綠漆問題分析
網印
PCB板面綠漆時為了加快印速增大產能之考量,硬化劑之外作業員還會加入調薄溶劑以稀釋之。常用者有“防白水”(BCS;Buty Cellosolve)與其他溶劑(如太陽公司自配的各種Reducer或他種原裝之PMA,PM等)。一般PCB板面
綠漆供應商建議,一公斤油墨中只能加15ml或1-3%(重量比)。黏度降低后不但好推好印,而且處在冷氣配合吹風的加工現場,其網布上的墨堆也較不易變干。
開罐待使用的油墨在加入硬化劑與稀釋劑后,為了整體黏度的均勻(以150PS為宜)起見,要利用螺旋槳式或L型劃槳(墨罐自轉)之攪拌器,或上下跳動之震蕩器等,緩攪半小時以上。有時為了趕工不免縮短攪拌或加快刮刀速度,或過量加入溶劑,或劇烈攪拌又未靜置消泡時,其網印硬化后的線路邊緣經常會有氣泡滯留。此種殘存氣泡非常明顯。每每被QA或客戶所拒收。
PCB板子在實地網印中也會產生氣泡,如刮印太快會產生氣泡,與刮刀走向呈橫置的密集平行線之“背風面”也容易藏氣,嚴重時“迎風面”也會有氣泡。通常背風面肩部的厚度很薄,該等間距之基材上甚至還會出現缺墨的Skip(跳印即漏印,可采去回多次刮印以解決之),一般與刮刀行程順向的密線區則較少出現氣泡。斜張網配合正貼擋墨點網版的方式,應可解決部分氣泡問題。氣泡常會發生在密線區的線邊,較少發生在空曠的板面上。以下分別用明視切片與暗視切片的放大照片佐證上述說法。
皆為100X之明視攝影,PCB板面綠漆雖未呈綠色但與其他材料仍能清楚分辨。
放大100X及200X之暗視攝影,其S/M層已清楚是綠色的畫面了。
一般網印法液態感光PCB板面綠漆(LPSM)的涂布,常在細密線路間出現氣泡。早期此時LPSM之配方尚不成熟時,亦曾流行一種“干膜式”的感光防焊皮膜。為了在很厚的線路上不被落差所剪斷起見,此種干膜之厚度在4mil左右。其施工法是以抽真空方式在板面上加溫壓貼,自然不會產生氣泡。下圖即為筆者13年前所做的切片,系碳酸鈉解像之杜邦商品Vacrel 8040。此防焊皮膜之密貼性及表面平坦性非常好,但可惜由于附著力不佳、施工麻煩、成本太貴,早已從量產線上遭到淘汰了。
不過最近P-BGA薄載板興起,要求PCB板面綠漆厚度在1mil以上且需塞孔平坦與杜絕氣泡,以防死角藏濕而遭“爆米花”的下游災難。此抽真空施工的“干膜PCB板面綠漆”似乎又有機會再現江湖。
200X之線路PCB板面綠漆,系采靜電自動噴涂法施工,不僅絕少氣泡且線肩厚度也在0.8mil以上遠超過規范所需。但漆料消耗卻頗大。
PCB板面綠漆厚度的重要
PCB板面綠漆的兩大任務是防焊與護線,后者正如具有絕緣皮膜所披覆的漆包線一般呈現護線功能。PCB板面綠漆因會隨著PCB板子出貨,其品質好壞除與下游組織有直接關系,且對最后產品也有深遠的影響。尤其新式的BGA與CSP類,不但須杜絕氣泡,更要求PCB板面綠漆的厚度。如此電路板在各種惡劣環境的用途中,可令導線不致被外界污染物所侵害,也才不致在可靠度(Reliability)方面出現危機。
PCB板面綠漆厚度于IPC-SM-840B規范中曾有明文規定,對Class 3 高可靠級的板類要求起碼厚度為0.7mil,對Class 2 的商用板類(如電腦與電腦周邊產品),其下限厚度定為0.4mil。但當840從B版修訂成C版時(1996.6),卻反而將原來厚度規格取消了。筆者對此一取消的看法,應該是為了訊號傳輸速度增快的考量。根據Maxwell公式,電磁波的傳播速度與光速(C)成正比,與波動傳播時所處介質之介質常數的開方值成反比(Dieleatric constant;又稱為相對介質透電率Relative Permitivity)。
而空氣與真空的相對透電率εr最低,均定為1,故在空氣中電波的速度等于光速。一般PCB板面綠漆的εr約在3.0(在1Mz頻率下所測得的數據),故PCB板面綠漆愈薄時(可接近空氣),方波訊號(也是電磁波的一種)的傳輸也愈快。因而高速電腦PCB板子對PCB板面綠漆的厚度也就不再強調了。
但當PCB板面綠漆厚度不足,尤其是針對較大電流而線寬又較粗的電源線時,則線路兩肩處的厚度仍應要求到0.4mil,以免在不良環境與通電工作中的加速腐蝕。電源線經組裝成品半年后透過厚度不足的PCB板面綠漆,被惡劣外界環境中的異物咬斷所致。切片中看到線路上的PCB板面綠漆厚度。
PCB板面綠漆太薄造成銅線遭腐蝕之10X畫面,板邊厚線路之PCB板面綠漆涂布。PCB板面綠漆對線路由左向右之刮墨印刷,注意刮前比刮后較厚情形。
早期之熔錫板,經下游組裝后原線頂熔錫層再次流動造成PCB板面綠漆起翹情形。右為PCB板面綠漆印于裸銅導線(SMOBC)上的密接與不受高熱影響之情形。
深圳宏力捷推薦服務:PCB設計打樣 | PCB抄板打樣 | PCB打樣&批量生產 | PCBA代工代料
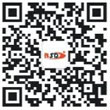