摘要:本文詳細介紹了
金相切片的制作過程,通過采用大量圖片和舉例的方式,論述了金相切片技術在印制
電路板生產中的應用,特別是在解決生產中出現質量問題方面的應用。
關鍵詞:金相切片 印制電路板 應用
印制電路板是電子元器件不可缺少的一部分,廣泛應用于電子行業,其質量可靠與否必須通過一定的檢測技術來判定。印制電路板制造工藝復雜,若其中某一環節出現質量問題,將導致印制電路板報廢。那么檢驗印制電路板須分過程中檢驗和成品檢驗。我們常用的檢驗手段有用放大鏡目檢,背光檢驗等。作為檢驗手段之一的金相切片技術,因其投資小,應用范圍廣,而被印制電路板生產廠家采用。金相切片是一種破壞性測試,可測試印制電路板的多項性能。例如:樹脂沾污,鍍層裂縫,孔壁分層,焊料涂層情況,層間厚度,鍍層厚度,孔內鍍層厚度,側蝕,內層環寬,層間重合度,鍍層質量,孔壁粗糙度等。總之,如同醫生用x 光給病人看病一樣,它可以觀察印制電路板表層和斷面微細結構的缺陷和狀況。本人在工作中對其有一定了解。現分幾方面簡述如下:
1. 金相切片(Microsectioning)的制作過程
金相切片制作工藝流程如下:
抽取待檢生產板→ 取樣→ 精密切割到符合模具大小→ 鑲嵌→ 粗磨→ 細磨→ 拋光→ 微蝕→ 觀測
1)生產線上抽取需做金相切片的生產板。
2)用剪床切取試樣中心和邊緣需做金相切片的部分。
3)使用精密切割機,切割試樣到符合裝模尺寸大小,注意保持切割面與待觀測面平行或垂直。
4)取一金相切片專用模具,將試樣直立于模內,讓待檢部位朝上。取一紙杯將冷埋樹脂(固態)與固化劑(液態)按2:1 體積比混合,攪拌均勻,倒入模具內,直到樣品完全浸沒,將模具靜置10-20 分鐘,待樹脂完全固化。
5)待固化完全后,先用較粗的金相砂紙將樣品磨至接近待檢部位,再按金相專用砂紙目數由小到大的順序進行粗磨和細磨。注意要磨到截面圓心的孔中央,且截面上兩條孔壁平行,不出現喇叭孔,樣品表面無明顯劃痕為止。
6)用拋光粉(粒徑0.05um),換上拋光布,對待檢表面進行拋光處理,使待檢表面光亮,無劃痕,通過顯微鏡可觀察到平整的待檢表面的圖像。
7) 用微蝕溶液(濃氨水和30%的雙氧水按體積比9:1 的比例混合)對待檢表面進行涂抹處理,時間約10 秒鐘,然后用清水將表面清洗干凈,吹干。
8) 將樣品的待檢部位朝下,平放于顯微鏡的觀測臺上,依據待檢部位的具體情況,選擇適當的放大倍數,直到能夠清晰地觀察其真實圖像為準。
2. 金相切片技術在印制電路板生產過程中的作用
印制電路板質量的好壞,問題的發生與解決,工藝的改進和評估,都需要金相切片來作為客觀檢查,研究與判斷的根據。
2.1 在生產過程質量檢測及控制中的作用
印制電路板生產過程復雜,各工序之間是相互關聯的,要最終產品質量可靠,則中間環節各工序的半成品板質量必須優良。如何判斷過程中生產板的質量狀況呢?金相切片技術將給我們提供依據。
2.1.1 鉆孔工序后的孔壁粗糙度(hole roughness)檢測
為保證印制電路板的孔金屬化質量,必須對鉆孔后的孔壁粗糙度進行檢測。可做試驗板,用不同大小的鉆頭鉆孔,取樣后,作金相切片,用讀數顯微鏡進行粗糙度的度量。為了使度量更準確,可將試樣進行金屬化孔后,再做金相切片。
2.1.2 樹脂沾污和凹蝕效果的檢測
印制
電路板鉆孔時產生瞬時的高溫,而環氧玻璃基材為不良熱導體,在鉆孔時熱量高度積累,孔壁表面溫度超過環氧樹脂玻璃化溫度,而產生一層薄的環氧樹脂沾污。多層板鉆孔后,若不經凹蝕就進行孔金屬化,將會造成多層板內信號線連接不通,而影響板的質量。通過制作金相切片,可以檢測到凹蝕后,樹脂沾污的去除效果,有利于控制多層板的質量。
2.1.3 鍍銅層厚度檢測
鍍層厚度往往是客戶對印制電路板的最基本要求,它包括基材銅箔厚度、鍍銅層厚度、孔壁銅層厚度、孔壁及表面鉛錫厚度(見圖4)。GJB 對鍍銅層厚度要求其平均厚度為25um,最小厚度20um。除可用測厚儀來測銅層厚度外,作金相切片,用讀數顯微鏡也可讀取其厚度,從而判斷是否符合國軍標要求。我廠采用Tiger3000 金相圖像分析軟件,可以準確測出孔內任何一處的銅厚及孔口表面銅層厚度,對孔內鍍層的判斷更直觀。
2.1.4 鍍層狀況檢測
將全板電鍍或圖形電鍍后的試驗板,制作金相切片,可檢測孔金屬化狀況,是否有鍍層裂縫,孔壁分層,鍍層空洞,針孔,結瘤等。
2.1.5 層間重合度檢測
為保證多層板層與層之間的圖形、孔或其它特征位置的一致性,層壓工序采用了定位系統。但某些因素的影響,會造成層間的偏離。為此,必須對多層板進行金相切片抽檢,以保證其符合質量要求。
2.2 在解決生產過程質量問題中的作用
印制電路板生產過程中,常常會發生各種各樣的質量問題。若借助金相切片技術能較快找到解決問題的原因,及時對癥下藥,采取有效措施,節約生產成本,保證按時交貨,贏得顧客的滿意。先將解決某些問題作一介紹:
2.2.1 鍍層空洞問題(plating void)
鍍層出現空洞問題,常會引起印制電路板業內管理人員的重視。造成鍍層空洞的原因多種多樣,而鍍層空洞的現象就有好幾種:①金屬化孔漏基材②金屬化孔內鍍銅層不大于板厚的5%③孔壁與各內環交接處出現鍍層空洞④孔內出現環狀孔破⑤楔形孔破等。出現以上現象的原因各異。其中孔內漏基材的原因就有很多。
如1)鉆孔粗糙挖破玻璃纖維布,以致深陷處不能完成孔金屬和電鍍銅層,2) 孔金屬化前處理不干凈,導致局部化學銅層無法導電,電鍍銅層無法鍍上,3)孔內有氣泡,在化學銅時,藥水無法浸潤而未沉上銅,4)孔內有雜質堵塞,無法沉上銅,5)藥液濃度、溫度未達到操作范圍,6)鍍層孔壁原本良好,因過分蝕刻后,銅層被腐掉,造成破孔。
現在選取典型的兩種問題來進行分析。
1.沉銅不佳。a.切片特征為:孔內出現對稱狀的環狀孔破,切片中可以看見圖形電鍍銅包裹著全板電鍍銅和化學銅。b.原因分析:對稱狀孔內無銅 :其實質為環狀無銅,是因為沉銅過程中,孔內有氣泡存在,使藥液與孔壁無法接觸,從而不能發生沉銅反應所致。
2.干膜入孔。a.切片特征:空口位置無銅,出現不對稱情況。b.原因分析:干膜貼膜后,板子停留時間過長,且為豎直方向放板,造成干膜流動進入孔內,在進行圖形電鍍時,該位置無法鍍上銅錫,退膜后此處的干膜被除掉,蝕刻時該位置的銅也被蝕刻掉,導致孔口無銅。
通過對有問題的板作金相切片分析,能有針對性的在相應工序采取對策,比如在對較小孔徑的板進行孔金屬化時,先檢測孔內有無殘渣,若有盡量吸干灰塵,配置振動和水平擺動裝置,增加溶液的過濾頻率,優化溶液參數,縮短干膜貼膜后板子的停留時間等。
2.2.2 側蝕問題(undercut)
多層印制電路板的外層圖形是通過蝕刻工序而得到的。當板經過蝕刻溶液,去除不需要的銅層,對于電鍍鍍厚的銅板,由于積液效應的存在,蝕刻液也會攻擊線路兩側無保護的銅面,造成象香菇般的蝕刻缺陷,對于正常的銅板在蝕刻時,蝕刻液不僅在垂直方向侵蝕線條銅層,同時會在水平方向腐蝕銅層,使蝕刻后的線條截面呈一個類似梯形,一般線底部寬于頂部,均稱為側蝕。側蝕的程度是以側向蝕刻的寬度來表示。
在生產中,側蝕若過于嚴重,將影響印制導線的精度,制作精細導線更不可行。而且側蝕易產生突沿,突沿過度,將會造成導線短路。通過制作金相切片,可以觀測到側蝕的嚴重狀況,從而找出影響蝕刻的原因加以改進。對于線寬/線間距為6mil 以上的板,蝕刻線寬控制上比較簡單,可增加底片線寬補償。而對于線寬/線間距4-5mil 的板,蝕刻線寬控制上則困難得多,一般以90%的板蝕刻干凈的速度來控制生產。為了減少其側蝕,通常采取嚴格控制銅濃度,PH 值,溫度和噴淋方式。比如蝕刻方式的影響,由潑濺改為噴淋,蝕刻效果好,側蝕也減小;蝕刻速率的調整,蝕刻速率慢會造成嚴重側蝕,便加快蝕刻速率;檢查蝕刻液PH 值,因PH 值較高,側蝕增大,就想辦法降低其PH 值;蝕刻液密度低也易造成側蝕,就選用高銅濃度的蝕刻液。經過有針對性的改進后,側蝕問題將得到很好解決。
2.2.3 鍍層分層問題
印制電路板生產廠家,在孔金屬化和圖形電鍍工序采用了大量藥液生產,若藥液體系不同,偶爾會出現鍍層分層的現象。分析其產生的原因,可能是印制電路板前處理效果不良,或藥液出現問題。究其產生的工序,離不開孔金屬化、全板電鍍和圖形電鍍工序。為解決問題,首先必須判斷問題產生的工序。此時,借助金相切片技術,可以清晰準確地找出產生問題的工序。因為金相切片試樣經微蝕后,基銅、全板電鍍銅和圖形電鍍銅可以清晰地區分開來,故根據鍍層發生分層的位置,就可找出發生問題的工序,從而縮小范圍,能更有效解決問題。下圖鍍層分層點在基銅與全板電鍍銅之間。分析原因是全板電鍍前表面處理不干凈造成的,更換前處理藥液后,分層現象未再發生。
2.2.4 鍍層斷裂問題
電鍍銅的鍍層厚度不足及鍍層性能不佳會導致鍍層斷裂(孔壁與內層互聯斷裂),鍍層厚度不夠(低于10 微米),吸潮后未烘板,在240℃熱沖擊下,也會造成鍍層斷裂。鍍層斷裂不僅影響了內外層電路互連,而且金屬化孔的耐焊性和拉脫強度也不符合質量要求。為了避免此類現象的發生,必須保證圖形電鍍銅厚大于25 微米,在120℃條件烘板2 小時后,再進行熱沖擊(熱風整平或焊接)。
根據電鍍理論科學,鍍層本身應力的大小將嚴重影響鍍層與基體的結合力。鍍層的內應力主要指宏觀應力,它分為張應力(+)和壓應力(-),張應力傾向使鍍層脫落,從而造成鍍層與基體分層;壓應力傾向于使鍍層向基體貼緊,從而提高鍍層與基體的結合力。銅離子和氯離子含量增加,鍍液溫度升高,鍍層的內應力會下降。而且鍍液中添加劑的含量會影響鍍層的延展性,添加劑、光亮劑等的分解產物溶解于鍍液中,去油不凈等有機物在電鍍槽過多都會使鍍層應力變大,延展性變差。因此鍍液成份和各工藝參數必須控制良好,才能有效提高鍍層的良好性能。否則鍍層在熱沖擊后容易在外層拐角處發生鍍層斷裂。
3. 結論
印制電路板的生產過程,是一個工藝流程復雜的,多工序間相互協作的過程。過程質量控制的好壞,將直接影響到最終產品的質量,在質量控制方面,金相切片技術發揮著重要的作用。此外,印制電路板生產中,總會出現這樣那樣的質量問題,要很好的解決這些問題,我們要有效利用金相切片技術,發揮它快速、準確的優點,準確找出問題的原因。在此基礎上,通過優化工藝參數,改進人為失誤,進行嚴格的生產管理,避免出現的質量問題再次發生,使印制電路板的生產質量穩步提高。由于本人的水平經驗有限,在此列舉了一些平時生產中遇到的實際問題,與同行共享和交流。
深圳宏力捷推薦服務:PCB設計打樣 | PCB抄板打樣 | PCB打樣&批量生產 | PCBA代工代料
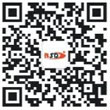